MESとERPの導入はどう違うのか?
どちらも、システム検討から含め長いプロジェクトであることは変わりありませんが、大きな違いは、MESは、現場向けのシステムであるということです。本ページでは、MESを現場に確実に定着していくまでの道のりとそのポイントをまとめました。
MESシステム導入の進め方(簡易チャート)
製造業においては、設備・装置による生産の自動化が進んでいる一方で、人が介在する業務においては、いまだに紙による記録管理業務が残されている実態があります。IT投資戦略の観点では、そうした「現場業務の生産性向上」「品質管理体制の強化」等の課題を解決する手段として、製造現場のデジタル化(デジタイゼーション)があります。本ページでは、現場の業務課題「製造記録の電子化」を掲げてシステム化に取り組むケースを例に、工場の現場にMESパッケージ製品を導入する手順をご紹介します。以下の図は、その取り組み全体を大きなPDCAサイクルで表したものです。
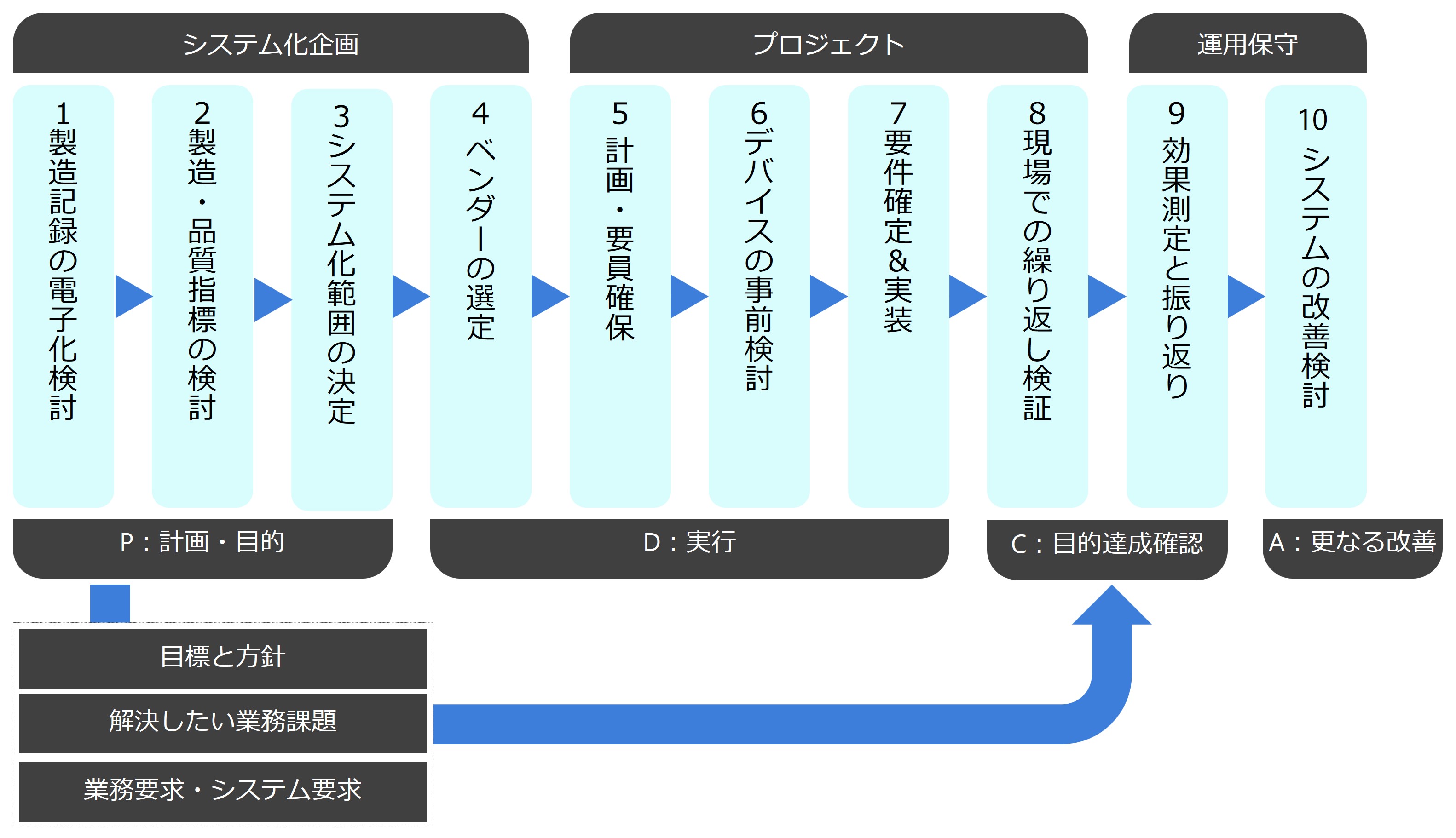
ステップごとのポイント解説
ここから、PDCAの流れにそって、1~10まで各ステップについてのポイントを解説します。
通常作業現場で「製造記録書」という紙に記載する場合、製造条件値や原料の使用料などを記載しているかと思います。これら製造記録項目のうち、どこまで電子化(パソコンでパッと見える)すればいいか検討します。
電子化する製造記録項目を使って、製造に関する指標や品質に関する指標を自動計算できるかどうか検討します。なお、その指標は製造クレームや生産性測定などに有効な指標であるかどうか検討します。これら指標の見える化が現場にとっての改善目的となります。
製造はたくさんの工程を通過して製品が製造されます。どの工程に対してシステム化するのか、どういう作業を間違えなく効率化できるのか検討します。この範囲のことをプロジェクトスコープといいます。製造・品質指標を検討しているので、そのスコープであれば指標が出せるのか矛盾ない範囲かどうか、再度思考します。
システム化の範囲(プロジェクトのスコープや実現したい要求事項など)が明確になったら、それらを取り纏め、その要求を実現できるベンダーを選定します。事前にRFI(Request For Information;情報提供依頼書)を発出し、ベンダー各社から情報収集を行います。その後、選定候補となるベンダーを絞り、RFP(Request for Proposal;提案依頼書)を発出し、ベンダー各社からの提案を募ります。提案内容、予算感、付き合っていけそうかなど判定基準に基づいて、ベンダーを選定しましょう。
無事にベンダーが決まりましたら、両社でスケジュール、必要な体制の確保、作業内容の確定を行います。重要なのは誰がプロジェクトをやるか、です。全体を取り纏めるプロジェクトマネージャー、何よりも現場を良く知る現場キーマンを選出して自社の製造工程をより良くしていけるメンバーを確保しましょう。
MESの導入で重要なのはデバイスです。製造現場で日々使うタブレットやPDA端末は、利用環境に合った機材を使わないと、すぐに使えなくなります。ベンダーに機材を推奨してもらい、デバイスメーカーから試用品を借りて、操作感などを確認しましょう。後から、これは使えないとなっては、本末転倒です。
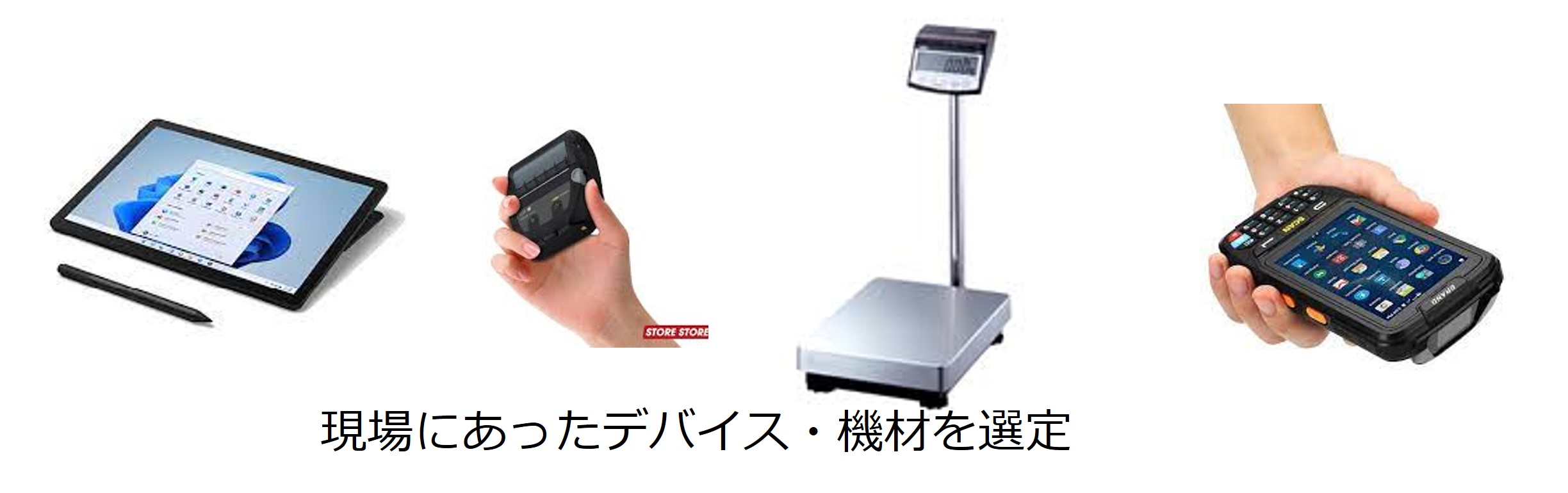
MESパッケージの導入では、要件定義において、実機を使った検証が重要です。実際のタブレット画面で必要なデータ登録が可能か、登録したデータが目的に見合った指標として使えるか、など実際の現場利用がイメージできるように、要件検討を行い、確定していきます。要件定義後は、必要な追加画面があれば開発をします。並行して製造オーダーの連携確認をしてデータがもらえるかなど検証して、テストに備えます。デバイスの現場への設置確認が必要です。まずはデバイスがシステムと導通できるのか、テスト前に現場調整を行い、確実に動くことを確認しましょう。
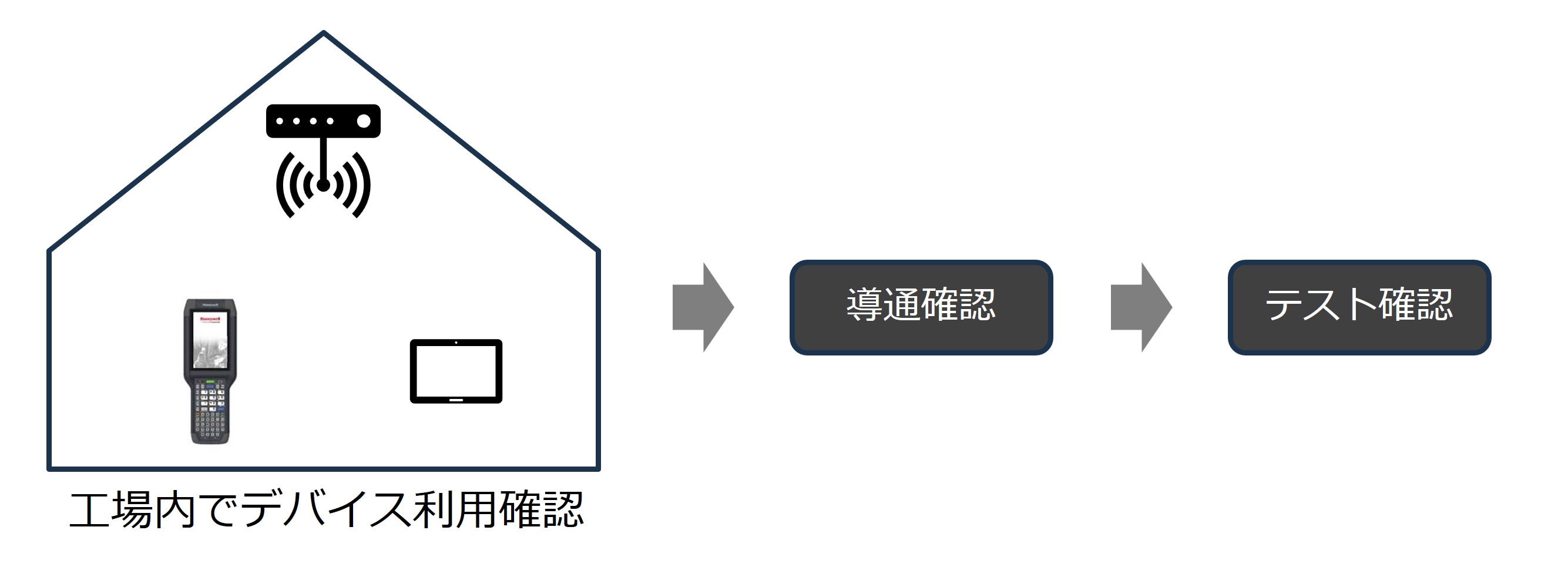
MESパッケージの導入、デバイスの設置が完了すれば、これからは繰り返し現場運用検証(テスト)を行います。実際のテストは本番運用と同じことを繰り返し検証してください。なぜなら、本番運用が始まれば、待ったなしです。工程の機械も止められませんし、作業も止められません。本番でのトラブルを避ける手段は、事前の繰り返し検証以外にありません。
無事にテスト検証を終えるとようやくカットオーバーを迎えて本番運用となります。稼働後、数日は慣れない作業も続き、戸惑いや時にはトラブルもあるかもしれませんが、不思議なことに徐々に慣れていき、通常運転となっていきます。システムは入れたら終わり、ではありません。通常運転が可能となってきたら、当初目的が達したのかどうか、効果測定を行ってください。必要としていた指標が見えるようになったのか、作業が以前よりもどのくらい早くなったのか、など、目的と照らし合わせて効果を確認してください。そして、十分に出来ていたのか、不足があるのか、振り返りをして報告にまとめましょう。
効果測定と振り返りが出来たら終わりではありません。改善は終わることが無いのが日本の製造現場の習慣です。当初目的を達していない箇所や、もっと良くなる機能などが見えてきたら、次の改善計画を立てましょう。運用で実現できることや、追加での投資が必要な改善もあります。計画的に現場改善を進めていくことが肝要となります。
お客様の導入事例をご紹介しています。システムの検討~構築~活用に関する成功事例を皆様のご検討にお役立てください。
ERPやMESの導入を検討している方に、取り組みのポイントをご紹介しています。